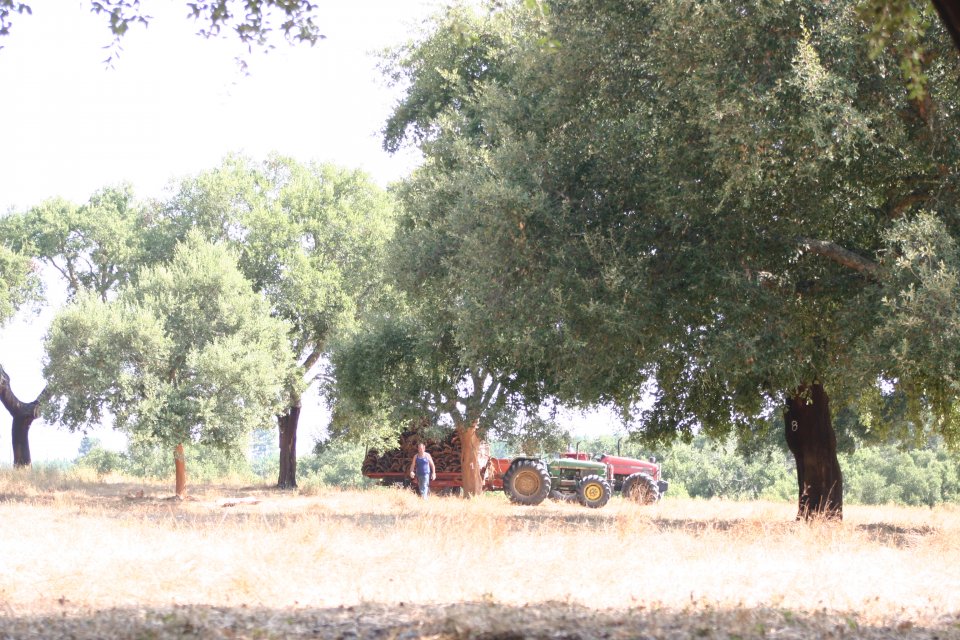
Improving the competitiveness of the cork oak producers, by improving the quality of the production process and the sustainability of the cork oak forest, by introducing new innovative methods and practices applied to the various stages of the production process and commercialization of the raw material, are essential to guarantee the vitality in the sector.
The profitability of the debarking, transportation and storage operations by promoting or increasing the efficiency of the processes along the potential value chain, with bring greater valorization of the raw material and improvements at the commercialization stage.
Despite the fact that Portugal is the main world cork producer and this continues to be an activity with great representativeness in national exports, cork is no longer an exclusive material for wine closure, with the appearance of alternative products, like plastic and aluminium for the same purpose. These changes may lead to a reduction in the economic value of the cork oak forests, representing a threat to the sustainability of these important landscapes and, consequently, to territories where their influence is decisive as an engine of economic development.
Already in 2005, PRIA (1) identified as a technological need: improving the logistics between debarking up to the factory.
Today, the main logistic issues that producers face are:
- Evaluation of available labor and proper hiring;
- Compatibility of labor availability with the optimal debarking season;
- Decision on stacking or loading with direct transport to the factory.
The option of stacking cork can be beneficial in situations where the initial humidity is lower and when the moisture discount normally associated with loading can become too penalizing in the business. In cases where the cork humidity in the debarking period is high, the option of stacking is less advantageous, since the costs of storing and insuring the pile have a very significant weight in this option.
Another factor to take into consideration will be the amount of cork to be harvested. Larger amounts dilute the costs/ unit and make the possibility of stacking more interesting.
1 - Know the cork moisture at the time of debarking, in the region;
2 - Consider the determining characteristics in the sale: the moisture discount conditions agreed with the buyer; the expected amount of cork to be harvested; the humidity of the cork at the time of extraction (make a moisture sample); the climate conditions of the year.
3 - Compare the two possible scenarios, based on reference data in the region and the conditions proposed by the buyer;
4 - Based on the previous points, decide on the model of the sales contract and the best form of commercialization (pile or loading).
Nowadays, as decades ago, cork extraction is carried out in the same way: manually, dropping the extracted planks of cork on the ground for later manual collection and transporting into a tractor trailer to the stacking location or loading directly to the factory. This direct transportation as increased mainly due to the partial relocation of the industries from the north to the south of Portugal.
The availability of two commercialization options (pile or direct transport) is not possible for all the forest managers due to the distance between the farm and the industry. High transportations costs, leave stacking as the only option economically viable.
Mechanical debarking will improve the quality of the extraction, reducing wounds on the trees, increasing the efficiency of the work and guaranteeing enough operators, minimizing the current problems - workforce scarcity and lack of training.
Alternative gathering models, namely with pallets, may replace the manual picking of the boards from the ground into the tractor, reduce the costs, also increasing the amount of cork transacted by the reduction of small pieces of cork originated by post-harvest handling.
Planning the harvesting progression in the farms and the extraction rails to be used by the tractor, using GPS and computer tools, will allow efficiency gains, and reduce fuel consumption.
Conceição Santos Silva, mcssilva@unac.pt, www.apfc.pt
Further information
- Augusto Mateus e Associados, 2005 – PRIA - Plano Regional de Inovação do Alentejo. CCDR Alentejo. ISBN 972-644-112-9.
- Lopes, M.V., 2018 - Fileira da cortiça: Estratégias diferenciadoras na fase pós colheita. FICOR – Feira Internacional da Cortiça.
- Sorensen, C.A., Larsen, P.G., 2017 - Off-line and on-line logistics planning of harvesting processes. Danish Innovation Foundation.
Conceição Santos Silva
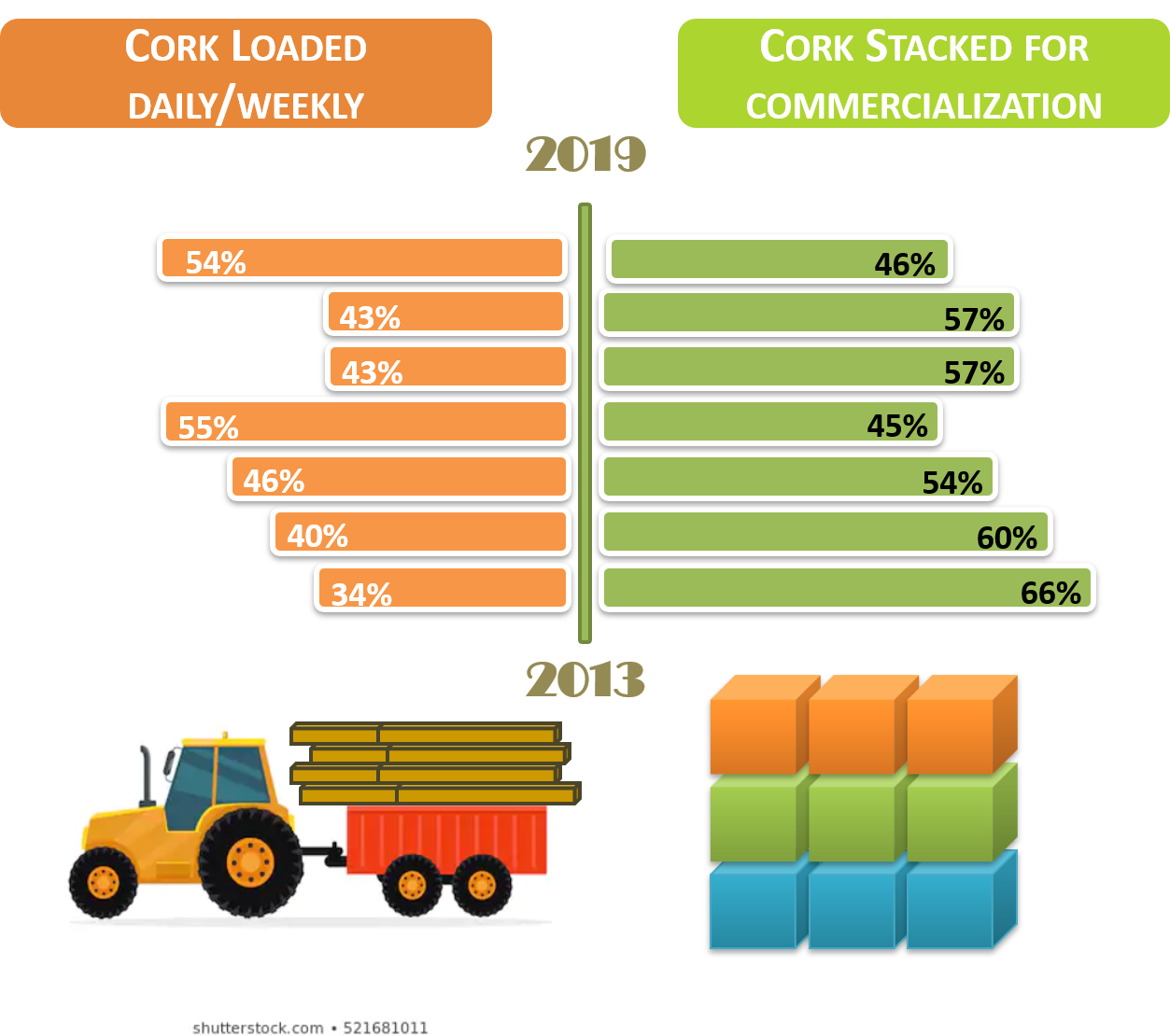
The extracted cork was traditionally stacked in the field and transported to the factory after 21 days. Nowadays, more and more producers choose the direct transport of cork to the factory on the day of extraction or the following days, avoiding the costs associated with the construction of the pile (labor, insurance, guard, etc.).
Credit: UNAC